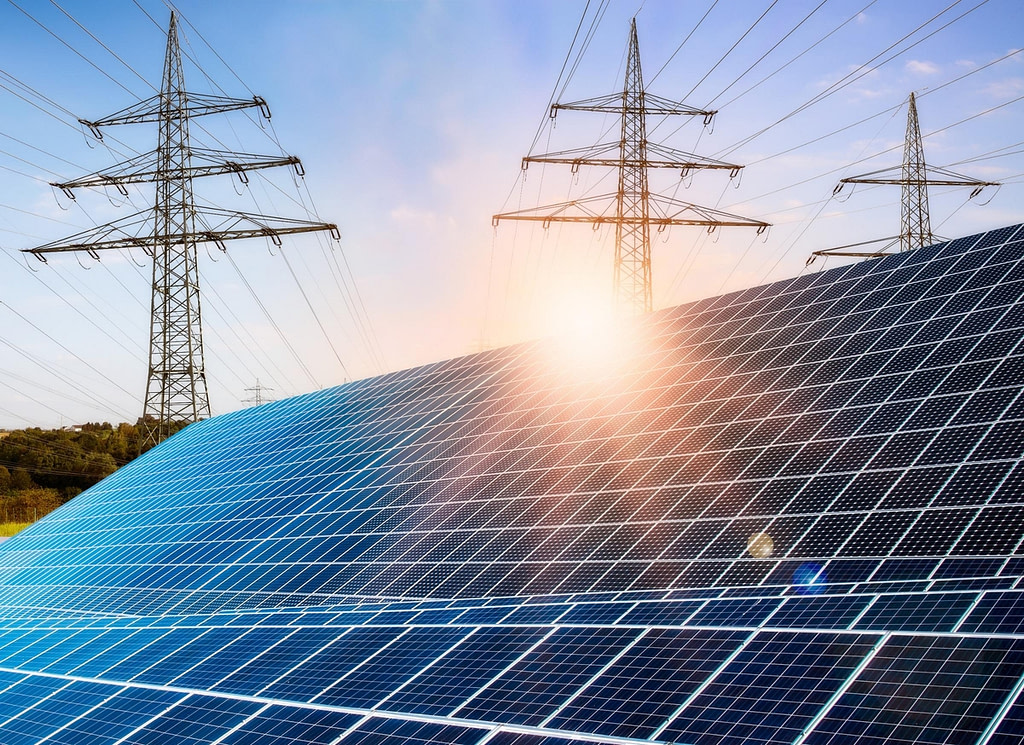
In addition to the industry and energy sectors, undetected partial discharges pose a threat to the operational safety and continuity of many critical areas of business and society. This article outlines how commonplace the occurrence of partial discharges actually is, and which operatives should pay extra attention to early-stage detection.
Partial discharges or PDs, as they are often referred to, are widely recognized as a serious threat in electrical systems. In fact, it has been estimated that up to 85% of electrical failures are related to partial discharges. While the existence of and need to detect partial discharges in industries like energy production and distribution seems fairly obvious, there are many sectors where the need for early stage detection is less apparent but equally critical. Do you know if the equipment that is vital for your business is prone to partial discharges? And if so, what kinds of risks your operations are exposed to and how are you best able to mitigate them?
Where and Why Do Partial Discharges Occur?
A partial discharge is a partial failure of an insulator that may in time progress and lead to complete insulator breakdown, causing severe problems, such as power outages and potentially hazardous accidents. All types of insulators, including solid, air, gas, vacuum, and liquid, are affected by partial discharges, which are most often divided into the categories of corona, floating, surface, and internal discharge, depending on where and how they occur. Common causes for partial discharges include the likes of surface contamination, material, manufacturing and installation defects, mechanical damages, and the wear and tear due to electrical stress. Simply put, partial discharges are caused by everyday phenomena and they occur just about everywhere where electrical systems are in use.

Which Industries Should Take Note?
The importance of addressing PDs early on is well acknowledged within the energy sector, but many other less obvious industries also benefit significantly from early-stage partial discharge detection. These include vital parts of infrastructure that rely heavily on electrical systems or even produce it through their own microgrid, like Pittsburgh International Airport. Other similar facilities include hospitals, ports, shopping centers, data centers, electric vehicle chargers, and public buildings. Another sector affecting our everyday life where partial discharges can wreak havoc on key systems and equipment if left unattended is utilities, such as water, gas, heating, and telecommunications. Also vulnerable to system failures are electricity-dependent heavy industries including mining, oil and gas, automotive, and aerospace as well as the manufacturing of products like metals, pulp and paper, food, and beverages. Given the scope of the many critical sectors of both business and societal life that are exposed to partial discharges, it is no wonder that their consequences are of equal proportions and often come with a hefty price tag. For instance, in steel manufacturing, the uninterrupted flow of electricity is an absolute must, and power outages caused by degraded components may lead to unplanned production halts costing hundreds of thousands of dollars.
How Does Predictive Maintenance Contribute to Meeting Regulation in the Electric Power Industry?
As interruptions in electricity supply have far-reaching consequences for society as a whole, it is understandable that electricity distribution is strictly regulated through international standards. These include the likes of SAIDI and SAIFI indices that compare electrical utilities’ performance reliability and IEC 60270 (ES), IEEE 1434-2014 (NAS), and GB/T 7354-2003 (GB/T7354-2003) (CHS) that monitor partial discharges in different types of electrical equipment, components, and systems.
To ensure that the standards are met, specialized predictive maintenance equipment is a must. As sound is one of the first indicators of electrical problems appearing even before components begin to heat up, we recommend using an acoustic device, such as the NL Camera, that detects both sonic and ultrasonic sounds caused by partial discharges even in noisy industrial environments. The camera is an efficient and easily implemented method for avoiding complete component failure that may lead to costly and often hazardous situations. Combined with AI-powered NL Analytics that recognizes the sounds partial discharges emit and distinguishes them from other sounds, pinpoints their exact location, automatically displays the PD pattern and indicates the strength and stage of the partial discharge, the NL Camera is a solution that makes intelligent cost and energy-saving maintenance decisions easier in any partial discharge-ridden environment.
For real life examples of how our customers have used our solutions for their predictive maintenance and repair needs, please visit our website!